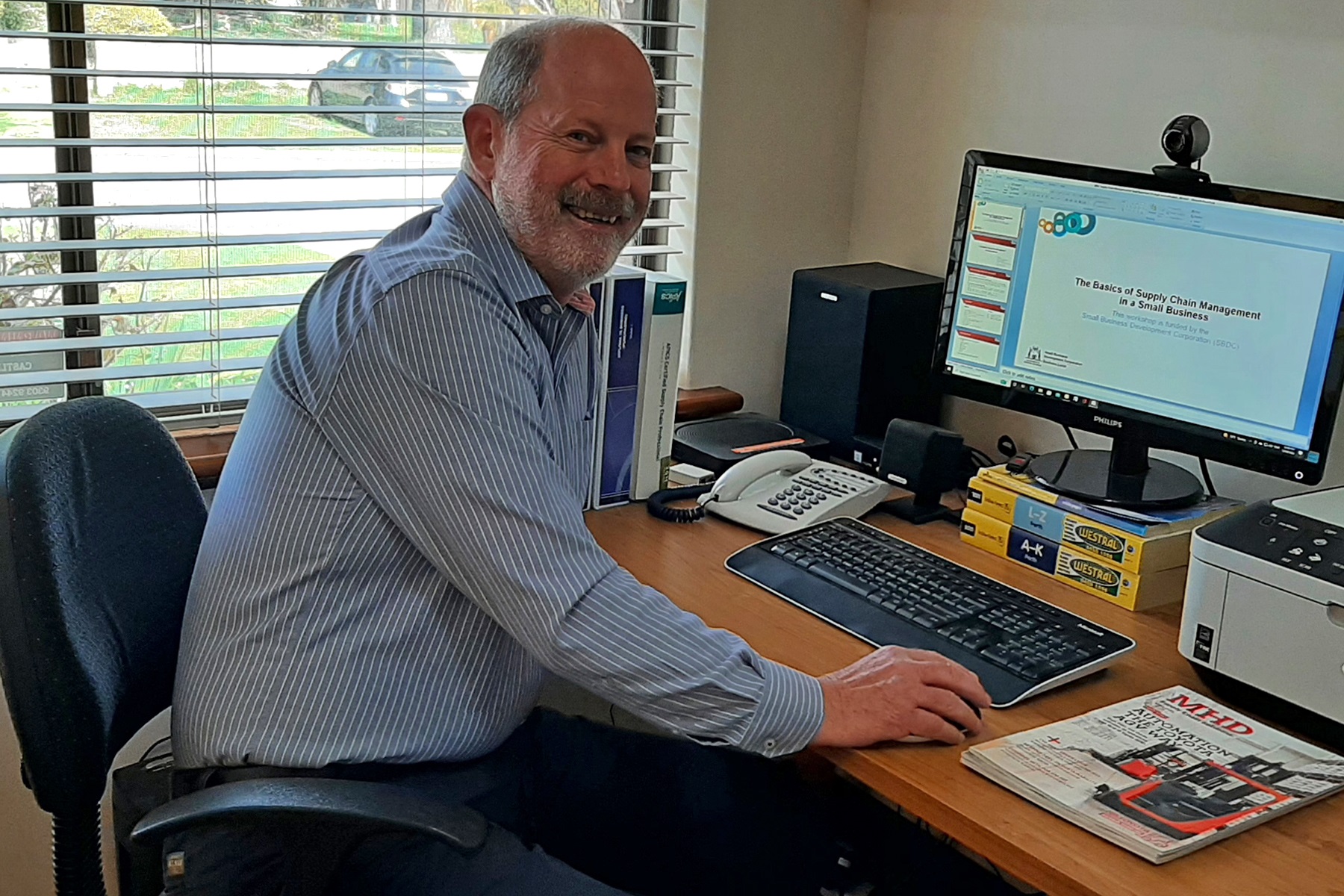
Supply chain management can be complicated. There will always be factors you can’t control including global events, economic conditions and industry challenges, which can impact your supply chain. To help support your business, it’s worth examining the risks involved along your supply chain and finding ways to streamline your processes.
Steve Murdoch from ECU is one of our SBDC workshop presenters and has been a supply chain manager for over 30 years in a variety of businesses. He is passionate about helping people understand the complexity of integrated supply chains and the use of Enterprise Resource Planning (ERP) computer systems to streamline this process.
We asked him for his top tips for small businesses working on supply chain management – and here’s what he shared.
Start by looking at the bigger picture
According to Steve, the basic principles of supply chain management apply to every business.
“All businesses have a supply chain, whether they buy and sell goods, make products or provide a service.” Steve says.
“To have more control over your supply chain, you need to examine its key components and the way they interact.”
Steve lists the key components of a supply chain as:
- the resources available, including people and Enterprise Resource Planning (ERP) computer systems
- your suppliers and management of these supplier relationships
- your procurement processes, including purchasing, goods inward and accounts payable processes
- inventory management, which involves having the right stock in the right place at the right time
- operations management, which includes any manufacturing processes in your business
- warehouse management from storing goods safely and efficiently, to picking and packing to fulfil your customer orders
- logistics, which can involve international, national and local transport, by air, sea and road.
With so many different processes, inputs and stakeholders involved in the supply chain, the risk of unexpected events or changes impacting your business is high.
Choose your areas of focus
“No business can avoid risk completely, but you can put strategies in place to mitigate risk across your supply chain,” explains Steve.
“Risk can be present with the suppliers you depend on, internally within your business and with your customers. It’s worth completing a risk analysis for these areas and developing strategies to mitigate the risks involved.”
Steve recommends you focus on developing strategies for the risks related to the top 20 per cent of your suppliers and customers. “This top 20 per cent is likely to make up 80 per cent of your spend and income – so a focus on these areas could be the best use of your resources.”
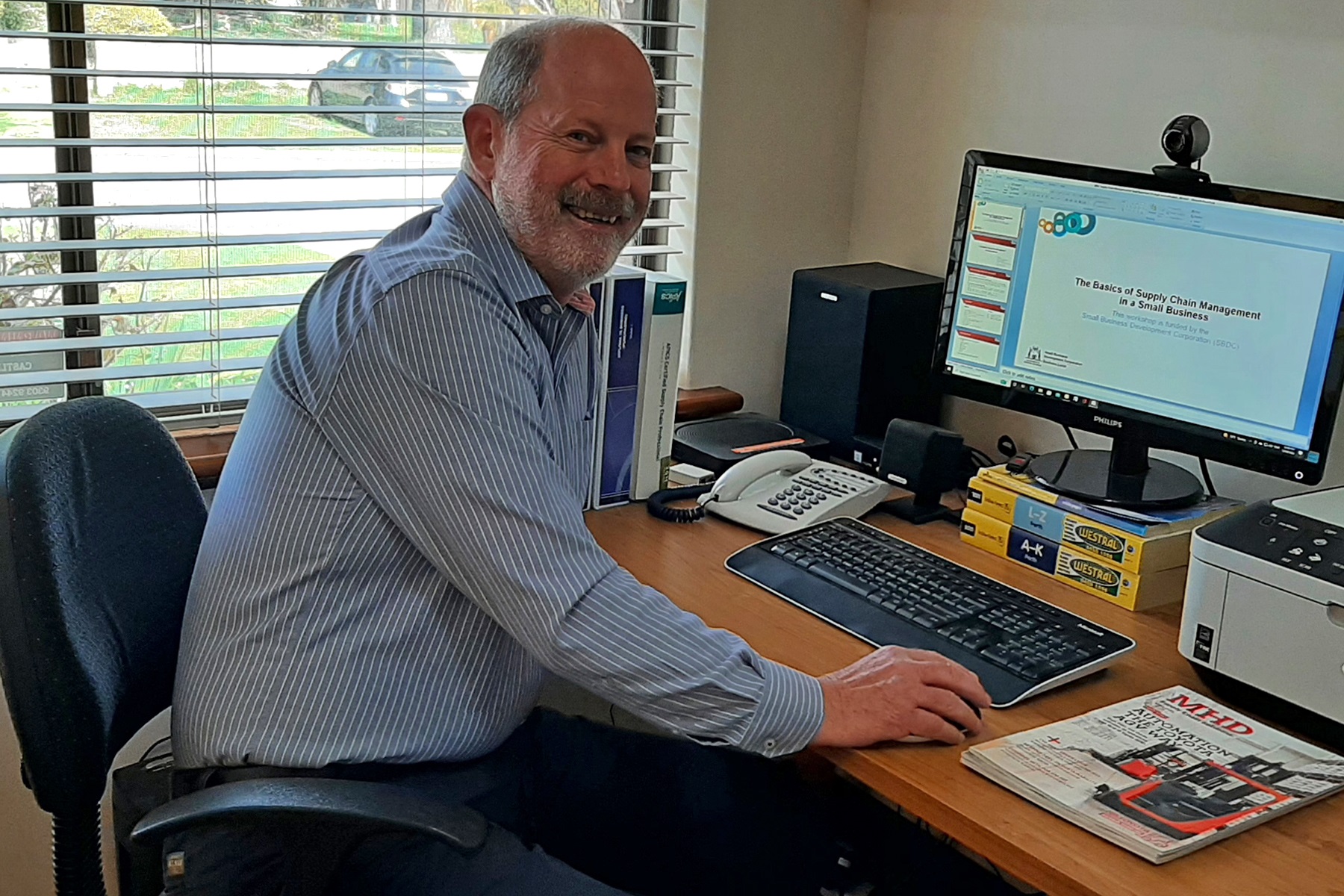
Have systems to manage demand
Common imbalances in the supply chain for a small business can be having too much stock (with the risk of not being able to sell it) or not enough stock to sell, perhaps because a supplier was unable to fulfill an order by a certain time.
Steve notes that to balance demand with appropriate supply and have the right inventory in the right place at the right time, all of the key areas of the supply chain need to be in sync.
“When your demand is seasonal – for example if you were selling agricultural parts – or certain items have long lead times or are coming from overseas, you need to forecast that demand.”
“Your demand might be created by a sales order to sell something, a work order to make something or a booking to provide a service. You need to have a system to look at your available inventory, and trigger orders such as purchase or work orders if you don’t have enough available stock.”
Automate your supply systems
Steve recommends making the most of your ERP computer system to manage the areas of your business which directly impact your supply chain activities.
“You must use your computer system to do this and set up all inventory items accordingly,” he says.
“For example, if your inventory is held in stock, the item needs to have re-order points set up in the computer item master that account for supplier lead times and safety stock.”
“If your inventory is not held in stock but only ordered on demand, this needs to be set up in the item master so the demand automatically triggers a purchase order from the appropriate supplier.”
Rely on your systems, not staff
There’s no doubt your team plays a vital role in the success of your business. Having supply chain systems in place can automate many activities, which can give you and your team more time to focus on your highest value activities.
Find out more
Streamlining your systems can give you more time to work on growing your business. Read about digital tools to boost your business which could help you manage your supply chain and other processes.
You might also like to explore our upcoming workshops or book an appointment with our free business advisory service to discuss your small business challenges.